Aus 150 angelieferten LKWs mit frisch geschlagenen Baumstämmen produzieren wir 2.000 Tonnen Hackschnitzel pro Tag im größten Hacker Europas. Ab hier beginnt dann die Produktion unserer „hochdichten Faserplatte“, abgekürzt HDF-Platte genannt.
Die Hackschnitzel werden in einem Hackschnitzellager mit einer Kapazität von 5 Produktionstagen gelagert, dadurch wird eine ununterbrochene Produktion an 365 Tagen im Jahr gesichert. Über verschiedene Fördertechniken werden die Hackschnitzel kontinuierlich dem nachfolgenden Produktionsprozess zugeführt.
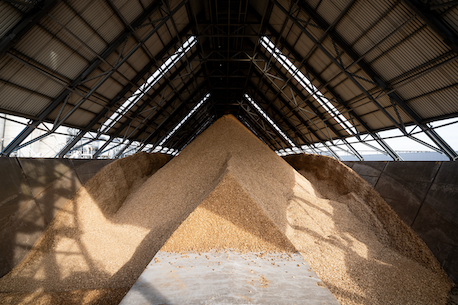
Zuerst werden die Hackschnitzel nach Größe gesiebt, dann gewaschen, entwässert, gekocht und zu Fasern zermahlen. Dies geschieht im sogenannten Refiner, in welchem zwei Mahlplatten die Hackschnitzel zu Fasern zermahlen. Mit Druck werden die Fasern anschließend in einem Rohr, der sogenannten „Blowline“, mit flüssigem Leim besprüht, um schließlich in einem riesigen Trockner mit Heißgasen weiter transportiert und dabei auch – wieder Name schon erahnen lässt – getrocknet. Das nachfolgende Sichten erfolgt über einen Luftstrom, wobei weniges schweres, für die Plattenproduktion ungeeignetes Material nach unten fällt, um dann als Brennstoff thermisch weiterverwendet zu werden. Die „Gut-Fasern“ kommen nun in den weiteren Produktionsprozess.
Hierbei werden die Fasern im Faserbunker zwischengelagert, bevor sie dann durch eine Austragseinheit abgetragen und über eine Streumaschine mit höchster Präzision zu einer gleichförmigen Fasermatte auf einem laufenden Förderband aufgestreut werden. Die sich so kontinuierlich bildende Fasermatte wird dann in der Vorpresse verdichtet und qualitativ überprüft. Und nun wird es für diese noch locker gebildete Fasermatte ernst: Sie wird in unserer 48 Meter langen Hydraulickpresse unter großem Druck und hoher Temperatur zu einem Endlosstrang gepresst. Wir können Plattenstärken von 5,3 mm – 13,0 mm herstellen.
Um diesen Endlosstrang nun auf das gewünschte Plattenmaß zu bringen (Standard: 2630 mm breit x 6190 mm lang) wird dieser seitlich besäumt und quer mit Diagonalsägen auf Länge aufgeteilt. Die so erzeugte, rechteckige Platte durchläuft ab diesem Zeitpunkt wichtige weitere Qualitätsprüfungen, durch die unsere Analgenfahrer frühzeitig auf Norm-Abweichungen reagieren können, wodurch wir unseren Ausschuss geringhalten. Dazu gehört auch, dass an stichprobenweise entnommenen Platten weitere Prüfungen in unserem internen Labor durchgeführt werden, um die erwartete, bestmögliche Qualität zu sichern und unseren Kunden ohne Mängel beliefern zu können.
Die auf Maß zurechtgeschnittene Platte verlässt jetzt, noch 60° Celsius heiß, die Presse und wird in Kühlsternwender, die aussehen wie überdimensionale Fächer, herunter gekühlt. Anschließend werden die nicht mehr ganz so heißen Platten in Großstapeln gesammelt und für 24 Stunden in ein sogenanntes „Reifelager“ gestellt, damit in dieser Zeit die chemischen Vorgänge innerhalb der Platte, gewollt ausgelöst durch den hohen Druck und die heißen Temperaturen, abgeschlossen werden.
Nach dieser Reifezeitzeit werden die Platten einzeln beidseitig geschliffen, wodurch die gewünschte Plattendicke auf den Zehntel Millimeter genau hergestellt wird. Ein abschließendes erneutes Besäumen und Sägen erzeugt dann auch nach Länge und Breite auf das gewünschte, kleinere Plattenmaß unserer fertigen HDF-Platte. Dies ist dann unser Endprodukt, welches nach weiteren Qualitätsprüfungen in Kleinstapeln geschichtet zu unserem Schwesternwerk Classen Industries GmbH transportiert wird, wo sie dann als sogenannte Trägerplatte dazu verwendet wird, um unseren Laminatboden herzustellen.
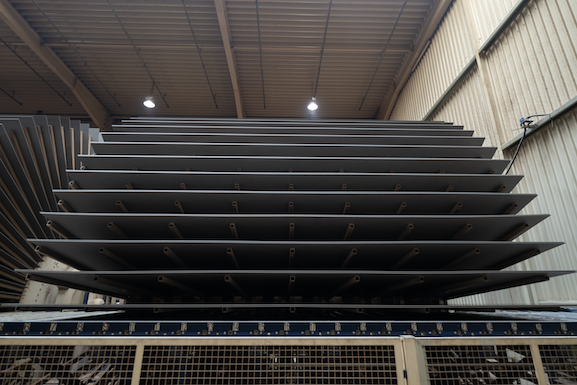
Findest Du auch, dass dies zwar kompliziert klingt, viele Fachbegriffe verwendet werden und es sich trotzdem nach einer spannenden Aufgabe anhört? Dann komm zu uns und starte durch mit unserem 9-monatigen Einstiegsprogramm.
Melde Dich bei uns und erfahre, was wir hier in Baruth bei Fiberboard ganz genau machen und wie man so etwas erlernen kann. Und wichtig: Du musst keinen bestimmten Berufsabschluss mitbringen, wir bilden Dich zu einem gesuchten und gut bezahlten Fachmann aus.
Nach Deiner Ausbildung bist Du Teil unseres kollegialen, hochqualifizierten Teams!